The term “rotor support stands” refers to various structures or devices that support, secure, or hold rotors or shafts in place. Rotors, which are rotating components, appear in many mechanical systems, including engines, turbines, and electric motors. People refer to rotor support stands by various names, such as Rotor Support Stand, Rotor Test Stand, Rotor Balancing Stand, Rotor Inspection Stand, Spindle Stand, Shaft Support Stand, and Rotating Equipment Stand. These stands provide a stable platform for rotors during maintenance, assembly, or testing. Dynamic Engineering Consultants have successfully completed numerous bespoke rotor support stand designs, each certified to meet the applicable Australian Standard. If you need this type of solution or something else, please contact us at info1@dynamicengineering.com.au or by using the “contact us” page by clicking the following link: https://www.dynamicengineering.com.au/contact-us/.
The specific design and function of rotor stands can vary based on the application and industry. Typically, you can find rotor stands used in aerospace, power generation https://www.sulzer.com/en/shared/campaign/gas-turbine-rotor-repair, and industrial machinery sectors.
Examples
Below are examples of rotor support stand designs by Dynamic Engineering Consultants:
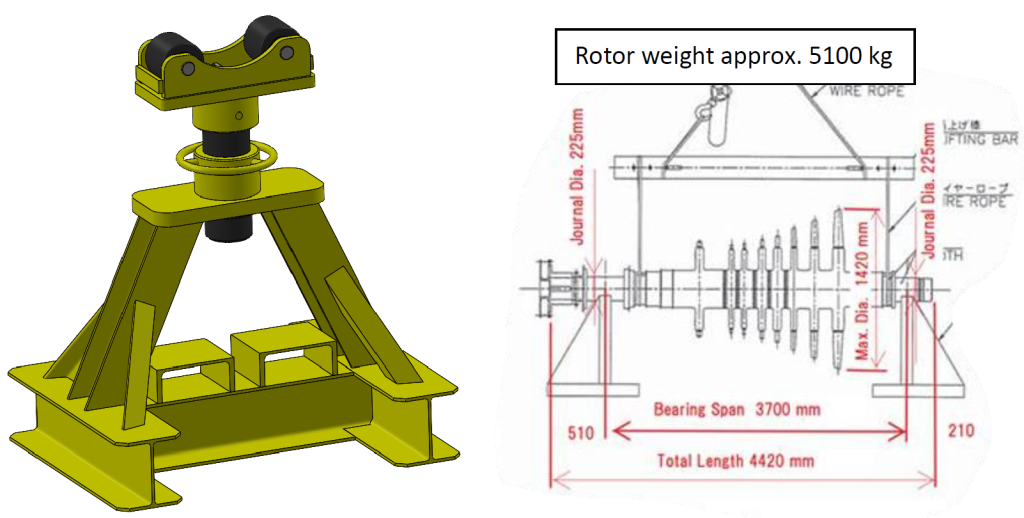
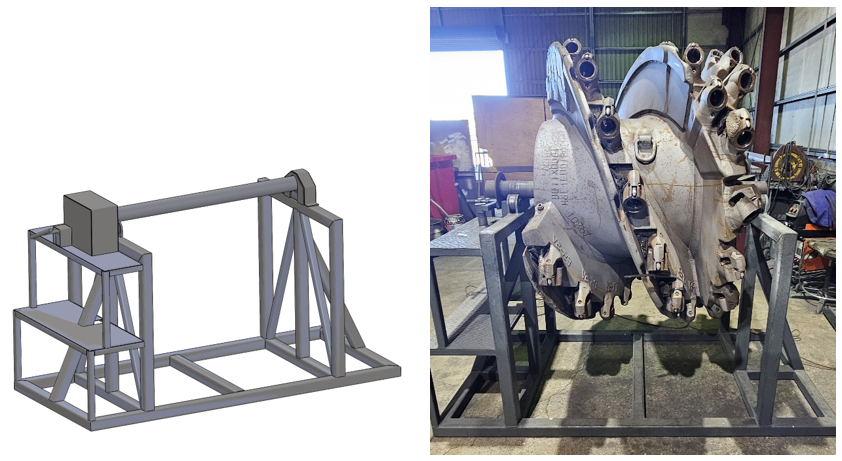
Why choose Dynamic Engineering Consultants for your rotor support stand designs?
Teaming up with Dynamic Engineering Consultants for your rotor support stand designs offers many benefits, particularly to ensure you have the right equipment for the job. In addition, using safe, certified equipment fundamentally promotes workplace safety, enhances product reliability, ensures regulatory compliance, and maintains a positive industry reputation. Consequently, this investment not only improves worker well-being but also prolongs equipment life, thereby contributing to overall business success. To illustrate, here are some detailed benefits:
Prevention of Accidents and Injuries: Certified equipment is designed, tested, and manufactured to meet specific safety standards, significantly reducing the risk of accidents and injuries for operators.
Compliance with Regulations: Many industries enforce strict regulations regarding equipment safety. Using certified equipment ensures compliance, fostering a safer work environment.
Consistent Performance: Certified equipment undergoes rigorous testing to guarantee reliability and consistent performance, which is crucial in critical applications where equipment failure could have severe consequences.
Quality Assurance: The certification process includes quality control measures, ensuring that equipment meets established standards for design, construction, and performance.
Reduced Liability: Using certified equipment can lower legal liabilities in case of accidents or injuries. It shows a commitment to safety and compliance with industry standards, which is vital in legal situations.
Insurance Compliance: Many insurance providers require businesses to use certified and safe equipment to qualify for coverage. Non-compliance can result in higher premiums or denial of coverage.
Customer Confidence: Utilizing certified equipment can enhance your business’s reputation. Customers, clients, and partners often trust organizations that prioritize safety and quality.
Reduced Downtime and Maintenance Costs: Certified equipment is generally more reliable, leading to decreased downtime and lower long-term maintenance costs.